Experience precision manufacturing with our Metal Injection Molding (MIM) services, including aluminum and stainless steel injection molding. machining, and metal insert plastic injection molding, provided by trusted and reputable suppliers and manufacturers.
XY-GLOBAL is dedicated to the medical industry, providing superior mechanical components and assemblies to match the reliability and performance of your medical industry products. We create value-added solutions for our medical industry customers through collaborative relationships, engineering expertise and innovation. We partner with leading medical and dental manufacturers to provide components for a variety of applications including precision surgical equipment, telemedicine equipment, diagnostic equipment, and dental equipment.
We are ISO 13485 certified!
XY-GLOBAL holds ISO 13485 certification, a management system standard designed for medical device manufacturing. This demonstrates that all medical device prototypes and components you receive from us are in full regulatory compliance. It also demonstrates our quality control and assurance system, assuring you that we will manufacture components to meet your specific needs. We are ready to serve every customer in the dental, biotech, surgical and other fields.
Why you should choose XY-GLOBAL for your medical manufacturing project
XY-GLOBAL is experienced.
XY-GLOBAL has in-depth knowledge and understanding of medical device manufacturing with over 10 years of experience. The medical industry is heavily regulated, so quality and precision are critical when manufacturing medical components and devices. Experience in medical device manufacturing is important, and XY-GLOBAL has the experience and expertise necessary to take your medical product from concept to final production.
Our team goes the extra mile.
When working with XY-GLOBAL, we are your trusted manufacturing partner, a complementary department, an informed advisor, not just a company that produces parts. We work with you to understand the ultimate goal of the device, the hierarchy of priorities and what it needs to do and how it needs to be executed - and give you insight into the best and most cost effective way to achieve it.
High-quality, high-end medical device manufacturing.
Medical device manufacturing experience is one thing, but ensuring the quality of the final product is another
1. Design analysis by modern CAD software and FEM tools to determine the best structure and performance of the product.
Design analysis is a critical step in the development of medical products and devices, and it requires a combination of factors, including the environment of use, ergonomics, materials and processes.
The design analysis process can use computer-aided design software to model, simulate and analyze the design. These tools can help designers and engineers better understand the performance and characteristics of the product, and identify and solve potential problems in a timely manner. For example, in the design of surgical instruments, computer-aided design software can be used to perform ergonomic analysis to ensure that surgical instruments can meet the surgeon's operational needs. During the analysis, different design options can be considered and the optimal one can be selected to achieve the best performance and quality. Iterative prototyping is a step-by-step approach to product improvement that helps development teams quickly verify the correctness of design and material selection in the early stages of product design and manufacturing. Through continuous feedback and adjustments, the reliability and performance of the product can be improved incrementally to ensure that it meets stringent medical standards and quality requirements. During this process, multiple versions of the prototype can be created using 3D printing, CNC machining and other prototyping tools for testing and evaluation. Each prototype can be used to validate designs and material choices, as well as to make design and material adjustments at different stages of product development. Through iterative prototyping, development teams can design and manufacture high-quality, high-performance medical products and devices faster. Design analysis is therefore an essential step in medical product and device development, helping to ensure that products are efficient, reliable, and safe. Our goal is to help save time and money - even if you need to make unplanned changes - to avoid unmanufacturable designs
2. Iterative prototyping methods are used to improve product reliability and performance
Iterative prototyping is a method of incremental product improvement that helps development teams quickly verify the correctness of design and material selection in the early stages of product design and manufacturing. Through continuous feedback and adjustments, the reliability and performance of the product can be incrementally improved to ensure it meets stringent medical standards and quality requirements. During this process, multiple versions of the prototype can be created using 3D printing, CNC machining and other prototyping tools for testing and evaluation. Each prototype can be used to validate designs and material choices, as well as to make design and material adjustments at different stages of product development. Through iterative prototyping, development teams can design and manufacture high-quality, high-performance medical products and devices faster.
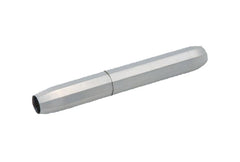
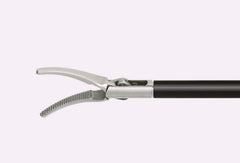
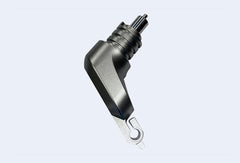
In the development of medical products and devices, the selection of materials is crucial. It is necessary to consider not only the mechanical properties, chemical properties, and biocompatibility of the materials, but also their long-term stability and resistance in the medical environment. For example, for medical devices implanted in the human body, it is necessary to choose materials that are non-toxic and non-carcinogenic, and can withstand factors such as corrosion and friction in the human physiological environment. In addition, medical products and devices require frequent disinfection and cleaning, so the materials selected must be able to withstand disinfectants and high-temperature and high-pressure cleaning processes.
In addition to factors such as mechanical properties and biocompatibility, the cost, availability and processability of materials are also important considerations in material selection. For example, in metal fabrication, certain metals may have desirable mechanical properties and biocompatibility, but be costly or difficult to process. Therefore, a combination of these multiple factors must be considered in material selection to find the most suitable material:
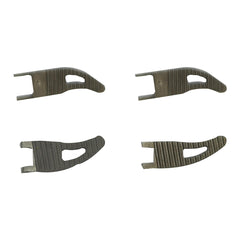
Stainless steel: Stainless steel has good corrosion resistance and biocompatibility, so it is widely used in the manufacture of medical devices.
Cobalt-chromium alloy: Cobalt-chromium alloy has high strength, high hardness and biocompatibility, and is widely used in the manufacture of artificial joints and dental implants, etc.
Titanium alloy: Titanium alloy has good biocompatibility and mechanical properties, so it is widely used in the manufacture of medical implants, such as artificial joints, bone plates and dental implants, etc.
Copper alloys: Copper alloys have good electrical and thermal conductivity and are widely used in the manufacture of pacemakers and other electronic devices.
Aluminum alloy: Aluminum alloy has good mechanical properties and corrosion resistance, and is widely used in the manufacture of medical devices and equipment shells, stents, etc.
In addition to material selection, subsequent handling and processing of the material needs to be considered. For example, in metal injection molding (MIM), the metal powder used must have good flow and sintering properties. Therefore, the selected metal powders must be specially treated to ensure their quality and performance. Factors such as cost and efficiency must also be taken into account when selecting materials and processing methods to ensure the quality and reliability of medical products and devices while meeting cost and productivity requirements.
●Laparoscopy
●Dental lathing needle
●Disposable surgical instruments
●Disposable implant molds
●Knife shaft tools
●Surgical clips
●Concept devices for surgery and implants
●Knives and scalpel shafts
●Cochlear implants
Our company has a rigorous process for every step from production to mass production. If you need custom metal injection molded parts, contact xy-global and we have a dedicated engineering team at market@mim-supplier.com to solve your problems and get high quality on-demand parts with professional prototyping and production capabilities. Instant quotes and automated DFM analysis can be completed online in seconds, and quality parts can be delivered in days.
Share:
Automobile Field Powered by Precision MIM Manufacturing from Trustworthy and Reputable Suppliers and Manufacturers