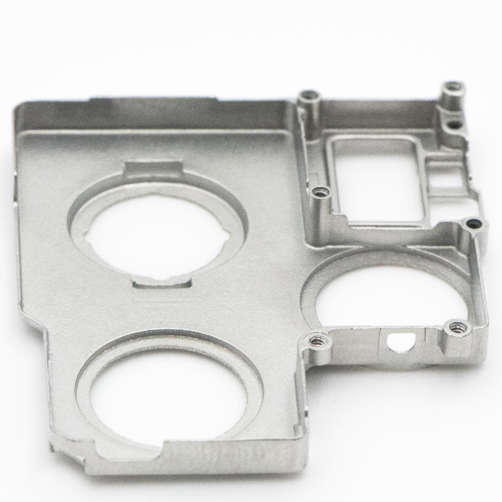
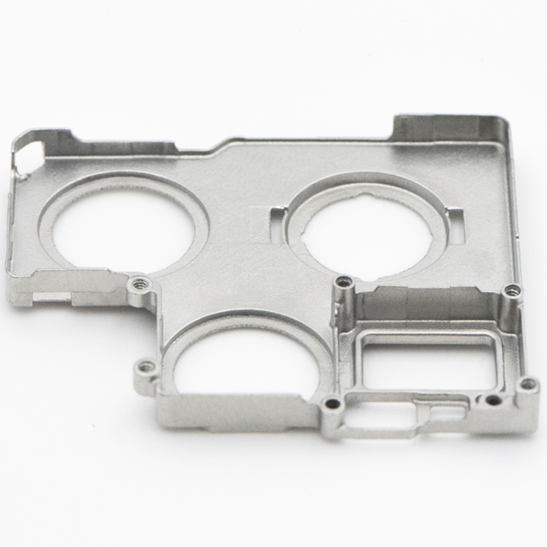
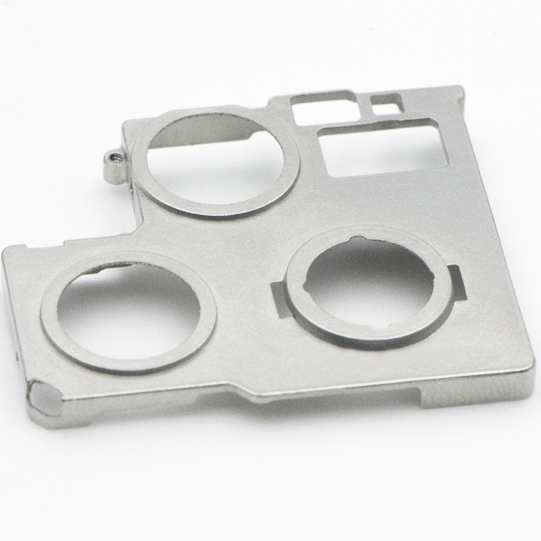
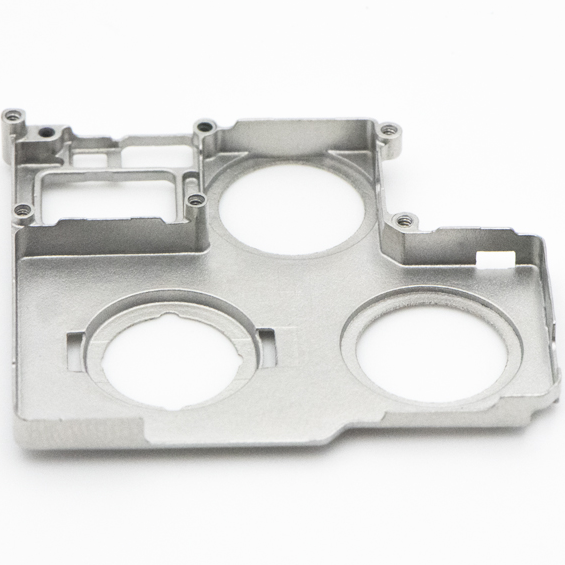
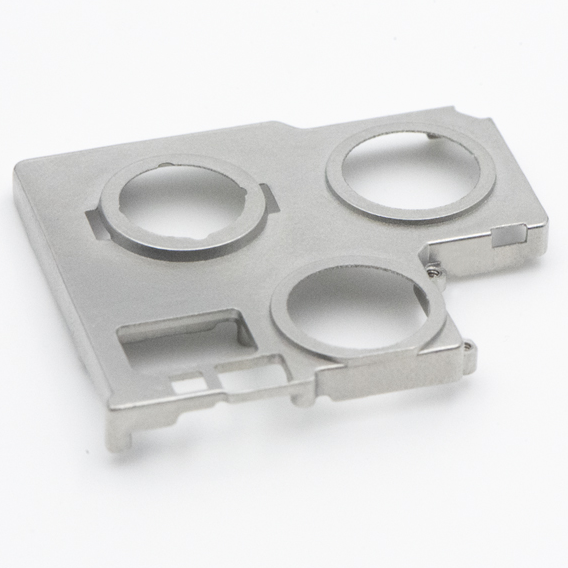
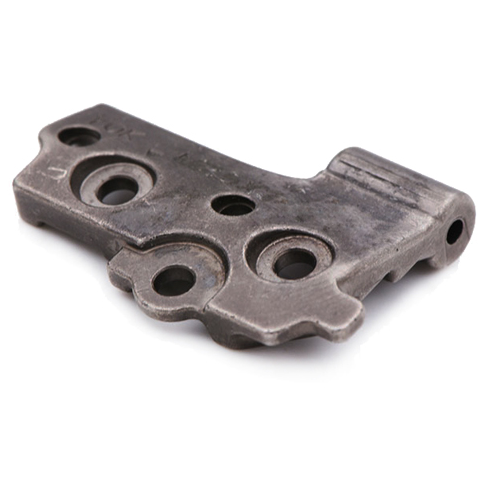
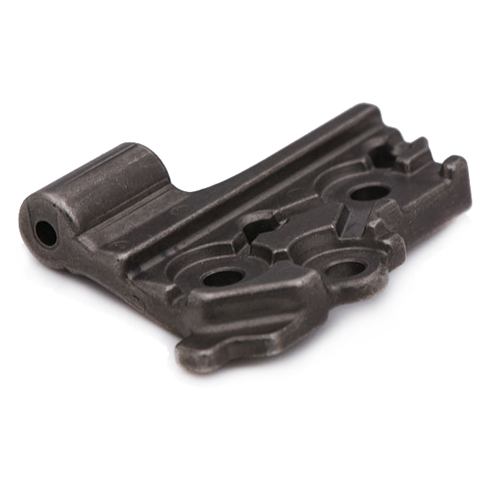
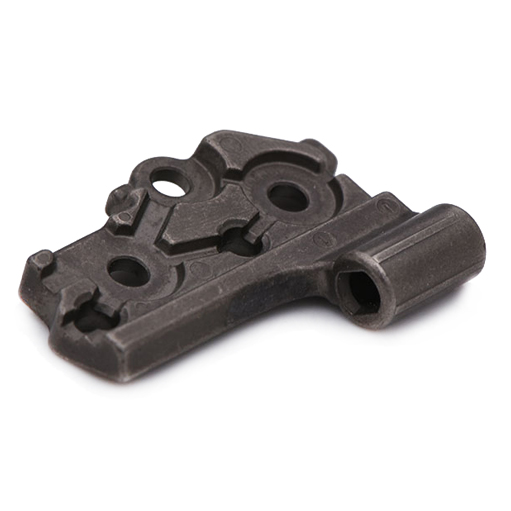
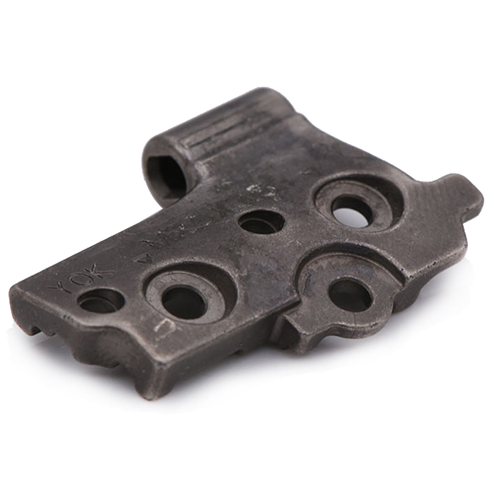
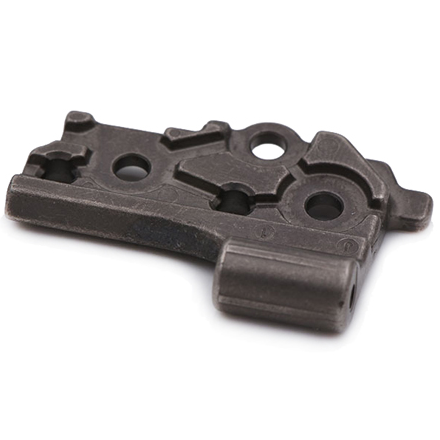
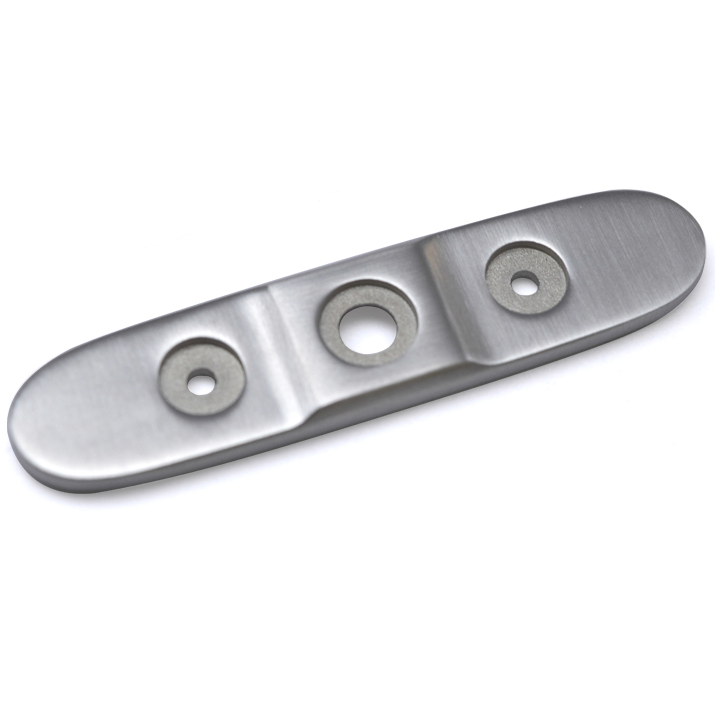

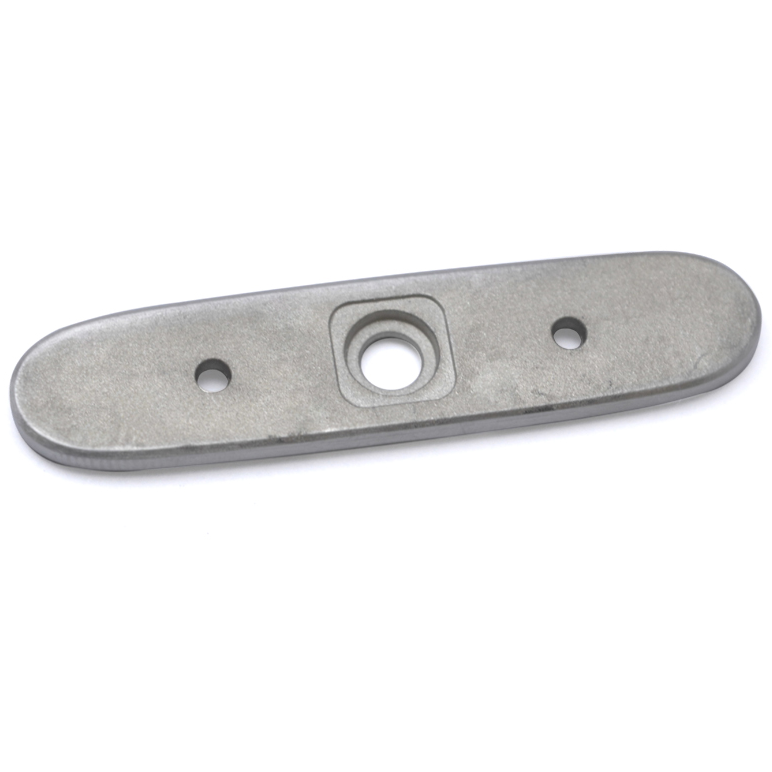
Aluminum Alloy Injection Molding Parts
Metal injection molding (MIM) is to uniformly mix powder and binder, then granulate the mixture through a granulator, and then inject it into the mold cavity to generate the desired shape. The mixed melt has good fluidity after heating, which is beneficial to the molding of the product during injection and maintains the density uniformity of the product. The formed products also need to be degreased and then placed in a sintering furnace for sintering. Some products also need some post-processing such as tapping, polishing, and coating.
However, problems arise if aluminum is used because the oxide layer around the aluminum particles can only be removed at extremely high temperatures. At the same time, the melting point of aluminum is relatively low, which limits the maximum sintering temperature. Therefore, it is impossible to remove the oxide layer on the aluminum powder before the entire metal piece is melted.
The binder material that binds the metal powders in the MIM feedstock is also removed by heat treatment, which only occurs when the temperature is increased. The overlapping temperature ranges for binder removal and sintering mean that if aluminum is processed using the same techniques as other metals, residues of the binder will be incorporated into the sintered workpiece.
A solution to this problem has now been successfully found. The key is to create the right atmosphere in the sintering furnace. A low-oxygen environment is usually used to prevent complete oxidation of metal powders. In contrast, for aluminum, an oxygen-rich atmosphere is beneficial. The particles have a very thick aluminum oxide layer that prevents complete oxidation of the particles. At the same time, oxygen helps burn the carbon component of the binder material.
After the first step, the oxygen atmosphere is replaced by nitrogen and the temperature is further increased. With the additional help of magnesium, the aluminum oxide layer is eventually destroyed and reduced. A liquid phase occurs and the aluminum particles are sintered to form solid metal sheets. This method allows the two processing steps to be separated; the removal of carbon residues and the sintering of aluminum particles, allowing both steps to be completed in the first run.
The aluminum alloy powder injection molding process can create complex shapes that are either impossible to achieve any other way, or require significant effort to achieve. Aluminum powder is relatively cheap, meaning even large components to MIM standards can be produced at a reasonable cost. Therefore, in large-scale production, material and weight savings of up to 50% are expected compared to conventional production.
This advanced technology is suitable for the production of large quantities of complex parts, including some extremely complex three-dimensional shapes, and the products produced do not require mechanical processing or require only a small amount of processing, which reduces production costs and improves production efficiency. Work efficiency.
If you have any questions, you are always welcome to contact us. We'll get back to you as soon as possible, within 24 hours on weekdays and weekends.
Customer Support
Your satisfaction is our priority.
We offer comprehensive Lifetime Technical Support and Warranty Services.
Contact Us
WhatsApp: +86 180 0255 3024
Email: market@mim-supplier.com
Shipping Information
We usually send samples to you via DHL FedEx or UPS.
Bulk goods will be shipped by sea to save shipping costs
FAQ’s
What materials do you provide?
We offer a wide range of materials for powder metallurgy.
MIM: 304 316 420 17-4 Stainless Steel, TC4 TA2 Titanium Alloys, AISI 310S Nickel-Chromium-Iron Alloys
CIM Process: Zirconia, Alumina, Silicon Nitride, Silicon Carbide, and Aluminum Nitride
Our R&D team can develop customized materials to meet your specific application requirements.